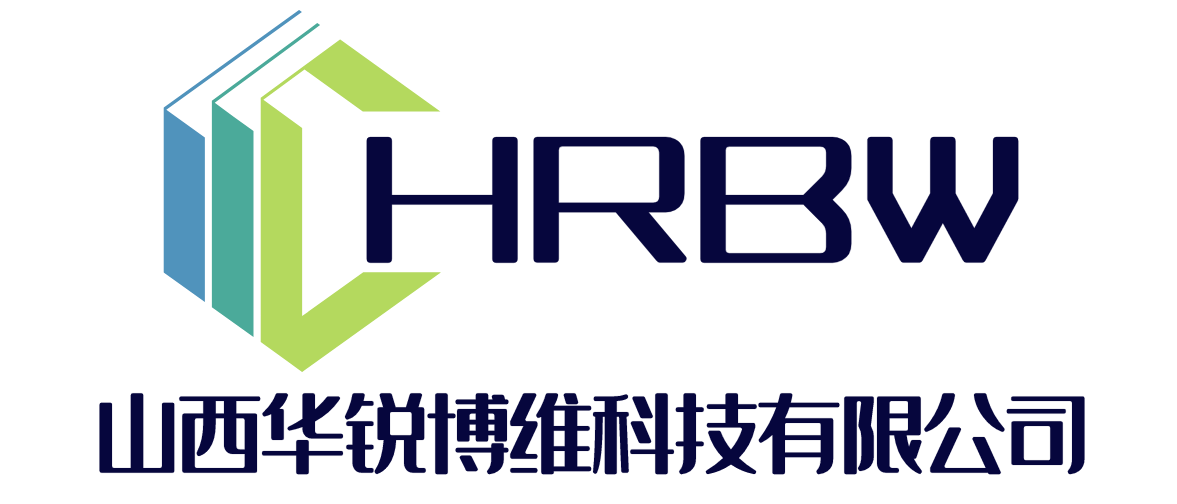
丙烷脫氫制丙烯工藝簡述
編輯:2022-03-01 16:57:03
丙烷脫氫制丙烯技術問世迄今已有20多年歷史,經過不斷完善,工業應用日趨成熟。
開發丙烷催化脫氫工藝成功的有:UOP公司的Oleflex 工藝、Lummus公司的Catofin 工藝、Snamprogetti公司的流化床(FBD)工藝、Uhde 的蒸汽活化重整(STA R)工藝、林德公司的PDH工藝。
采用較多的是美國UOP公司的Oleflex工藝和Lummus的Catofin 工藝。兩種丙烷脫氫制丙烯工藝大體相同,所不同的只是脫氫和催化劑再生部分。
1
Oleflex I藝
UOP公司的Oleflex工藝是20世紀80年代開發的,1990年首先在泰國實現了工業化,1997年4月韓國投產250 kt/a丙烯的聯合裝置采用第2代Oleflex技術。目前,全Oleflex丙烷脫氫制丙烯總生產能力達2500kt/a。在國內煙臺萬華建成最大的750kt/aPDH裝置。
Oleflex工藝利用富含丙烷的液化氣(LPG)作原料,在壓力為3.04 MPa,溫度為525℃,鉑催化劑作用下脫氫,經分離和精餾得到聚合級丙烯產品。進料前需要預處理。Oleflex采用移動床技術,由反應區、催化劑連續再生區、產品分離區和分餾區組成。
將預處理的C3液化氣原料進入脫丙烷塔中,C3液化氣中一些丁烷或較重組分從脫丙烷塔底部排出,脫丙烷塔塔頂餾出物送入Oleflex裝置,生產出富含丙烯的液體產品和富含氫氣的氣體產品。純凈氫氣可直接輸出,濃縮成化學級產品,也可作為聯合裝置內的燃料。來自
Oleflex裝置的液體產品送入選擇氫化(SHP)裝置,除去二烯烴、乙炔。SHP產品送入脫乙烷塔,除去在Oleflex裝置生成的或新鮮C3液化氣含有的輕質尾氣,以及溶解在Oleflex液體產品中或進入SHP裝置的少量氫氣。脫乙烷塔底部純凈的產品直接送到丙烷-丙烯(P-P)
分離塔,在此把丙烯產品和未轉化丙烷分開。在P-P分離塔底部的未轉化丙烷經過C3液化氣原料脫丙烷塔循環到Oleflex裝置。P-P分離塔出來的丙烯產品純度通常達99.5%~99.8%。丙烯產率約為85%,氫氣產率約為3.6%。
Oleflex工藝設計的主要特點是采用移動床反應器,反應均勻穩定,催化劑活性長久保持不變,催化劑再生時反應器不需要關閉或循環操作,同時,連續補充催化劑。氫氣為稀釋劑,用以抑制結焦、抑制熱裂解和作載熱體維持脫氫反應溫度。
含有烴類的反應器部分和含有氧氣的再生部分是一體化,但還安全地保持著分離。使用鉑催化劑,具有高活性、高選擇性和低磨損率,由于可靠和精確CCR再生控制,Oleflex催化劑具有很長的服務壽命并提供優良的產量穩定性。Oleflex技術使用無鉻(Cr)無致癌催化劑。該技術移動床技術復雜,投資和動力消耗較高。為了增強Oleflex工藝的競爭能力,UOP公司進行了多次改進,主要集中在催化劑方面,已有DeH-8、DeH-10、DeH-123代新催化劑工業化,DeH-12催化劑在選擇性和壽命有較大的提高,鉑含量比DeH-10少25%,比DeH-8少40%。使用新催化劑操作空速提高20%,減小反應器尺寸,待再生催化劑上的焦含量低,可使再生器體積縮小50%,可減少投資,降低成本。
2
Catofin 工藝
Lummus公司的Catofin 工藝是ABB Lummus公司開發的C3~Cs烷烴脫氫生產單烯烴技術。目前,有10家采用Catofin工藝生產烯烴,生產量超過3200kt/a。
Catofin工藝分為4個工段:丙烷脫氫制丙烯、反應器排放料的壓縮、產品的回收和精制。Catofin工藝利用逆流流動技術改變了反應物料流向,空氣向下、烴類直接向上,能以較少的原料獲得較多的產品,從而減少了投資及操作費用。采用鉻/鋁催化劑,其組分包括質量分數大于18%的氧化鉻,這種催化劑的脫氫性能穩定,烷烴轉化率高,循環量少,每100t丙烷原料可制76~86t丙烯。固定床反應器內以烴類/熱空氣循環方式操作,采用多個反應器連續操作。烴類進入催化劑床層前,用熱風預熱,在650℃、0.05MPa左右條件下進行反應。該技術丙烷的轉化率≥90%,丙烯選擇性超過87%。進料不需要預處理。但該工藝效率較低,能耗較大。
3
FBD 工藝
Snamprogetti公司的FBD工藝是在俄羅斯開發的硫化床脫氫制異丁烯基礎上發展起來的,其技術核心是反應器-再生系統,反應和再生是在硫化床中完成的,FBD技術對應俄羅斯一套130kt/a異丁烯裝置進行技術改造,另有5套異丁烷和丙烷脫氫項目選擇該技術。
4
PDH I藝
德國Linde(林德)、BASF與挪威國家石油公司合作開發的PDH工藝,主要生產丙烯和異丁烯。
采用裝填催化劑的多管式固定床反應器,按烴類/熱空氣循環方式操作,反應段有3臺氣體噴射脫氫反應器,2臺用于脫氫操作,1臺用于催化劑再生。在反應溫度為590℃、壓力為33.9~50.8kPa的條件下,丙烯轉化率大于90%。采用Cr203/Al2O3催化劑在590℃、壓力大于0.1MPa條件下操作,對PDH技術進行了2年多的測試后采用BASF提供的Pt/沸石催化劑對工藝進行改進,在Statoil公司位于挪威的煉廠完成了中試驗證試驗,單程轉化率由32%提高至50%,總轉化率則由91%提高至93%。PDH技術具有產量高、裝置體積小、基建要求低等特點。
5
STAR I藝
STAR工藝是由Philips石油公司開發,2000年被Uhde收購并進行了改進。STAR藝采用固定床管式反應器和專有Pt和Ca-Zn-Al2O3為載體催化劑,在500~640℃,0.1~0.2MPa,水蒸氣存在條件下進行反應,輕質石蠟脫氫轉變為烯烴。水蒸氣的作用是降低反應物的分壓、促進反應、減少催化劑表面積炭。專有Pt催化劑具有高的選擇性和單程轉化率,丙烷脫氫過程的單程轉化率為30%~40%,丙烷生成丙烯的選擇性為80%~93%,丙烯收率約80%。與其他丙烷脫氫工藝相比,STAR工藝具有催化劑用量少、反應器體積小等優點。
Uhde公司已對該工藝進行了驗證試驗。推出STAR工藝用于輕質烷烴氧化脫氫為烯烴,采用蒸汽活化轉化技術。并在2006年實現工業化,投建了埃及350kt/a丙烯和聚丙烯聯合裝置。該工廠2010年投入使用,運行穩定,工藝過程易于操作,顯示出極佳的經濟性。
此外,伍德公司還簽約了另外3家規模更大的丙烷脫氫裝置合同。中東地區2套450ktPDH裝置以及美國1套54.40kt的PDH裝置。
6
新型丙烷/丁烷脫氫(ADHO)技術
新型丙烷/丁烷脫氫(ADHO)技術,是重質油國家重點實驗室的又一項催化劑和反應器配套研發的重要成果。
采用無害的非貴金屬催化劑,減少了對環境和操作人員的毒害及投資費用。丙烷單程轉化率為41.28%,丙烯收率和選擇性為33.03%和80.01%。ADHO技術采用循環流化床反應裝置,可實現連續反應再生。
ADHO技術的主要優勢:催化劑,無腐蝕性,機械強度高,劑耗低;催化劑裝量少,一次性投入要低得多;原料無需凈化,含烯烴、正丁烷等都不影響裝置的正常運行,適用于丙烷與異丁烷單獨脫氫,也適用于混合脫氫;可長期穩定運行;裝置規模不受限,投資少;不需要在臨氫條件下反應。在山東恒源石油化工完成工業化試驗證明,填補了國內該技術領域的空白。目前Oleflex及Catofin工藝已有多套工業應用,技術比較成熟,STAR 工藝剛進行工業化應用。早期丙烷脫氫多用Oleflex 工藝,且是整套轉讓,初期投資費用較高。Oleflex工藝烯烴收率穩定,催化劑再生方法理想,催化劑使用壽命長,裝填量少;但由于Catofin工藝采用Cr203/Al2O3催化劑,且鉻系催化劑穩定性差,具有毒性,不環保,開發低Cr含量的催化劑才有一定的前景。
丙烷脫氫制丙烯工藝簡述
編輯:2022-03-01 16:57:03
丙烷脫氫制丙烯技術問世迄今已有20多年歷史,經過不斷完善,工業應用日趨成熟。
開發丙烷催化脫氫工藝成功的有:UOP公司的Oleflex 工藝、Lummus公司的Catofin 工藝、Snamprogetti公司的流化床(FBD)工藝、Uhde 的蒸汽活化重整(STA R)工藝、林德公司的PDH工藝。
采用較多的是美國UOP公司的Oleflex工藝和Lummus的Catofin 工藝。兩種丙烷脫氫制丙烯工藝大體相同,所不同的只是脫氫和催化劑再生部分。
1
Oleflex I藝
UOP公司的Oleflex工藝是20世紀80年代開發的,1990年首先在泰國實現了工業化,1997年4月韓國投產250 kt/a丙烯的聯合裝置采用第2代Oleflex技術。目前,全Oleflex丙烷脫氫制丙烯總生產能力達2500kt/a。在國內煙臺萬華建成最大的750kt/aPDH裝置。
Oleflex工藝利用富含丙烷的液化氣(LPG)作原料,在壓力為3.04 MPa,溫度為525℃,鉑催化劑作用下脫氫,經分離和精餾得到聚合級丙烯產品。進料前需要預處理。Oleflex采用移動床技術,由反應區、催化劑連續再生區、產品分離區和分餾區組成。
將預處理的C3液化氣原料進入脫丙烷塔中,C3液化氣中一些丁烷或較重組分從脫丙烷塔底部排出,脫丙烷塔塔頂餾出物送入Oleflex裝置,生產出富含丙烯的液體產品和富含氫氣的氣體產品。純凈氫氣可直接輸出,濃縮成化學級產品,也可作為聯合裝置內的燃料。來自
Oleflex裝置的液體產品送入選擇氫化(SHP)裝置,除去二烯烴、乙炔。SHP產品送入脫乙烷塔,除去在Oleflex裝置生成的或新鮮C3液化氣含有的輕質尾氣,以及溶解在Oleflex液體產品中或進入SHP裝置的少量氫氣。脫乙烷塔底部純凈的產品直接送到丙烷-丙烯(P-P)
分離塔,在此把丙烯產品和未轉化丙烷分開。在P-P分離塔底部的未轉化丙烷經過C3液化氣原料脫丙烷塔循環到Oleflex裝置。P-P分離塔出來的丙烯產品純度通常達99.5%~99.8%。丙烯產率約為85%,氫氣產率約為3.6%。
Oleflex工藝設計的主要特點是采用移動床反應器,反應均勻穩定,催化劑活性長久保持不變,催化劑再生時反應器不需要關閉或循環操作,同時,連續補充催化劑。氫氣為稀釋劑,用以抑制結焦、抑制熱裂解和作載熱體維持脫氫反應溫度。
含有烴類的反應器部分和含有氧氣的再生部分是一體化,但還安全地保持著分離。使用鉑催化劑,具有高活性、高選擇性和低磨損率,由于可靠和精確CCR再生控制,Oleflex催化劑具有很長的服務壽命并提供優良的產量穩定性。Oleflex技術使用無鉻(Cr)無致癌催化劑。該技術移動床技術復雜,投資和動力消耗較高。為了增強Oleflex工藝的競爭能力,UOP公司進行了多次改進,主要集中在催化劑方面,已有DeH-8、DeH-10、DeH-123代新催化劑工業化,DeH-12催化劑在選擇性和壽命有較大的提高,鉑含量比DeH-10少25%,比DeH-8少40%。使用新催化劑操作空速提高20%,減小反應器尺寸,待再生催化劑上的焦含量低,可使再生器體積縮小50%,可減少投資,降低成本。
2
Catofin 工藝
Lummus公司的Catofin 工藝是ABB Lummus公司開發的C3~Cs烷烴脫氫生產單烯烴技術。目前,有10家采用Catofin工藝生產烯烴,生產量超過3200kt/a。
Catofin工藝分為4個工段:丙烷脫氫制丙烯、反應器排放料的壓縮、產品的回收和精制。Catofin工藝利用逆流流動技術改變了反應物料流向,空氣向下、烴類直接向上,能以較少的原料獲得較多的產品,從而減少了投資及操作費用。采用鉻/鋁催化劑,其組分包括質量分數大于18%的氧化鉻,這種催化劑的脫氫性能穩定,烷烴轉化率高,循環量少,每100t丙烷原料可制76~86t丙烯。固定床反應器內以烴類/熱空氣循環方式操作,采用多個反應器連續操作。烴類進入催化劑床層前,用熱風預熱,在650℃、0.05MPa左右條件下進行反應。該技術丙烷的轉化率≥90%,丙烯選擇性超過87%。進料不需要預處理。但該工藝效率較低,能耗較大。
3
FBD 工藝
Snamprogetti公司的FBD工藝是在俄羅斯開發的硫化床脫氫制異丁烯基礎上發展起來的,其技術核心是反應器-再生系統,反應和再生是在硫化床中完成的,FBD技術對應俄羅斯一套130kt/a異丁烯裝置進行技術改造,另有5套異丁烷和丙烷脫氫項目選擇該技術。
4
PDH I藝
德國Linde(林德)、BASF與挪威國家石油公司合作開發的PDH工藝,主要生產丙烯和異丁烯。
采用裝填催化劑的多管式固定床反應器,按烴類/熱空氣循環方式操作,反應段有3臺氣體噴射脫氫反應器,2臺用于脫氫操作,1臺用于催化劑再生。在反應溫度為590℃、壓力為33.9~50.8kPa的條件下,丙烯轉化率大于90%。采用Cr203/Al2O3催化劑在590℃、壓力大于0.1MPa條件下操作,對PDH技術進行了2年多的測試后采用BASF提供的Pt/沸石催化劑對工藝進行改進,在Statoil公司位于挪威的煉廠完成了中試驗證試驗,單程轉化率由32%提高至50%,總轉化率則由91%提高至93%。PDH技術具有產量高、裝置體積小、基建要求低等特點。
5
STAR I藝
STAR工藝是由Philips石油公司開發,2000年被Uhde收購并進行了改進。STAR藝采用固定床管式反應器和專有Pt和Ca-Zn-Al2O3為載體催化劑,在500~640℃,0.1~0.2MPa,水蒸氣存在條件下進行反應,輕質石蠟脫氫轉變為烯烴。水蒸氣的作用是降低反應物的分壓、促進反應、減少催化劑表面積炭。專有Pt催化劑具有高的選擇性和單程轉化率,丙烷脫氫過程的單程轉化率為30%~40%,丙烷生成丙烯的選擇性為80%~93%,丙烯收率約80%。與其他丙烷脫氫工藝相比,STAR工藝具有催化劑用量少、反應器體積小等優點。
Uhde公司已對該工藝進行了驗證試驗。推出STAR工藝用于輕質烷烴氧化脫氫為烯烴,采用蒸汽活化轉化技術。并在2006年實現工業化,投建了埃及350kt/a丙烯和聚丙烯聯合裝置。該工廠2010年投入使用,運行穩定,工藝過程易于操作,顯示出極佳的經濟性。
此外,伍德公司還簽約了另外3家規模更大的丙烷脫氫裝置合同。中東地區2套450ktPDH裝置以及美國1套54.40kt的PDH裝置。
6
新型丙烷/丁烷脫氫(ADHO)技術
新型丙烷/丁烷脫氫(ADHO)技術,是重質油國家重點實驗室的又一項催化劑和反應器配套研發的重要成果。
采用無害的非貴金屬催化劑,減少了對環境和操作人員的毒害及投資費用。丙烷單程轉化率為41.28%,丙烯收率和選擇性為33.03%和80.01%。ADHO技術采用循環流化床反應裝置,可實現連續反應再生。
ADHO技術的主要優勢:催化劑,無腐蝕性,機械強度高,劑耗低;催化劑裝量少,一次性投入要低得多;原料無需凈化,含烯烴、正丁烷等都不影響裝置的正常運行,適用于丙烷與異丁烷單獨脫氫,也適用于混合脫氫;可長期穩定運行;裝置規模不受限,投資少;不需要在臨氫條件下反應。在山東恒源石油化工完成工業化試驗證明,填補了國內該技術領域的空白。目前Oleflex及Catofin工藝已有多套工業應用,技術比較成熟,STAR 工藝剛進行工業化應用。早期丙烷脫氫多用Oleflex 工藝,且是整套轉讓,初期投資費用較高。Oleflex工藝烯烴收率穩定,催化劑再生方法理想,催化劑使用壽命長,裝填量少;但由于Catofin工藝采用Cr203/Al2O3催化劑,且鉻系催化劑穩定性差,具有毒性,不環保,開發低Cr含量的催化劑才有一定的前景。
電話:4006228811
郵箱:longcai@126.com
傳真:400-681-8888
地址:哈爾濱市道里區愛建路13號